Penetrant Testing (PT)
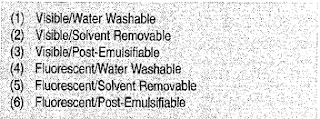
Penetrant Testing (PT) In general terms, penetrant testing reveals surface discontinuities by the bleedout of a penetrating medium against a contrasting colored background. This is accomplished by applying a penetrant (usually liquid) to the cleaned surface of the test piece. Once this penetrant is allowed to remain on the surface for a prescribed time (dwell time), it will be drawn into any surface opening by capillary action. Subsequent removal of excess penetrant and application of a developer draws remaining penetrant from discontinuities. The resultant indications are shown in high contrast and magnify the presence of the discontinuity so it can be visually interpreted. There are two primary ways in which penetrant materials are grouped: specifically, the type of indication produced, and the method of excess penetrant removal. The two penetrant indications are visible and fluorescent. The visible dye (usually red) produces a vivid red indi...